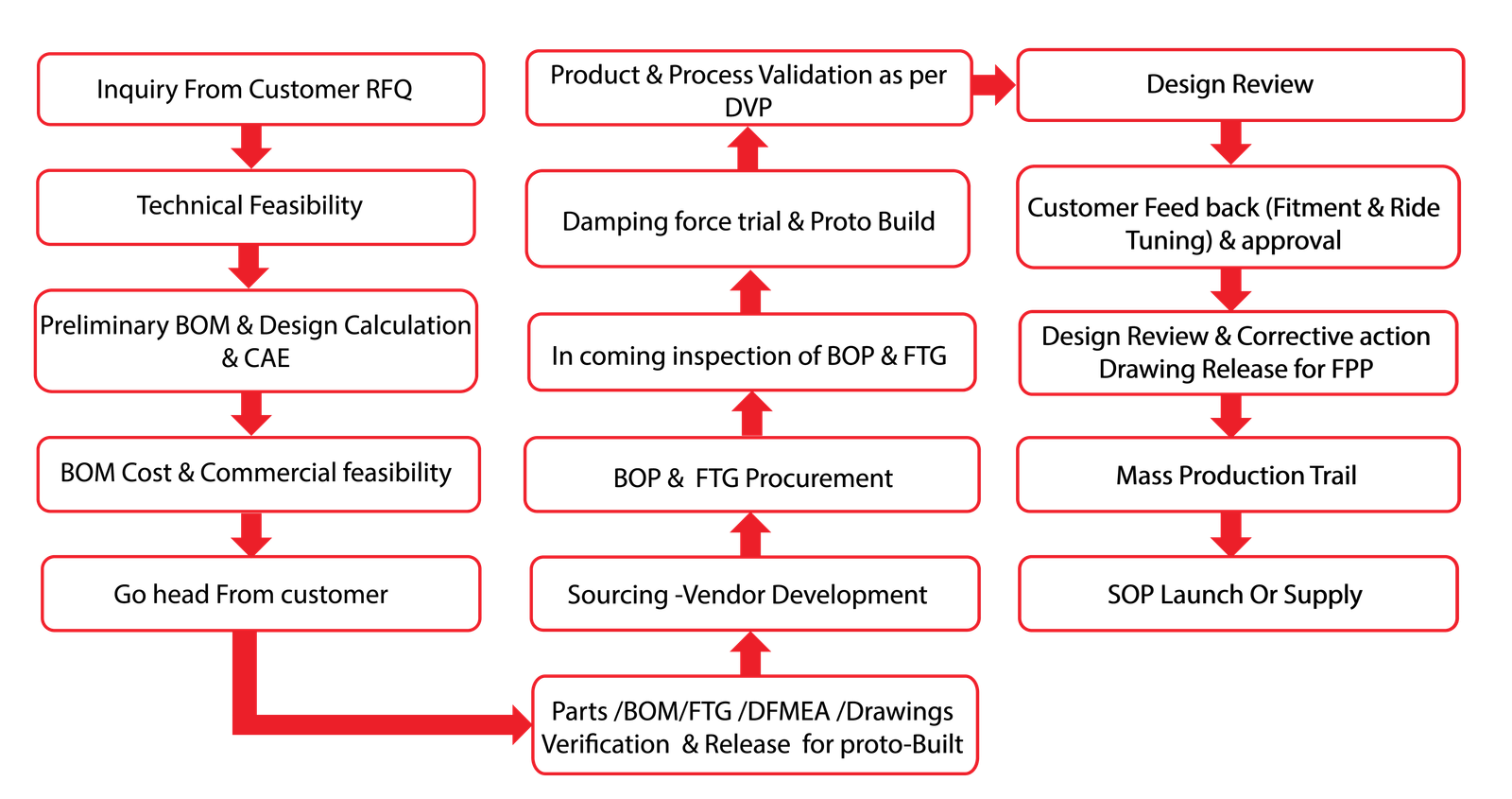
MSL Innovation Center
The R&D Centre is responsible for using state-of-the-art technology, developing comprehensive know-how and engineering capabilities, and designing and developing suspension products for both OEM customers and aftermarket.
The R&D centre is capable of performing CAE analysis through R&D software and concluding robust solutions during the design and development phases of the products. The anticipated innovative solutions and analysis results are validated by performing actual validation tests with the R&D test equipment available with us.
The R&D Test Centre consists of the following:
Shock absorber, front strut, front fork damping force testing machine (MTS), and several shock absorber, front strut, and front fork durability testing machines with provision for side load application.
These testing machines are used during the design and development phase of the shock absorbers, front struts, and front forks in order to validate the design of the product in terms of specified damping force values and the expected product life applicable to each application.
The complete front suspension assembly and rear suspension assembly of a two-wheeler are mounted on a drum roller to simulate actual road conditions and continuously run to establish the life of the assembly as well as the individual parts.
This equipment measures the reaction forces of the front strut, front fork, and gas-charged shock absorbers.
The shock absorber is cycled at different velocities, and the noise levels are measured to confirm that they are within allowable limits. The test is warranted to ensure passengers’ comfort.
A specified weight is dropped down on the complete assembly of a front fork or front strut from a specified height, and the capacity of the assembly to withstand the impact is studied.
A specified weight is dropped down on the complete assembly of a front fork or front strut from a specified height, and the capacity of the assembly to withstand the impact is studied.
MEASUREMENT LAB
Coordinate measuring machines contribute to eliminating potential mistakes in measurements as a validation method for R&D projects related to both aftermarket and OEM customers. Therefore, the product design can be completed reliably and effectively.
The optical emission spectrometer covers the analysis of the chemical elements in the complete range from sub-ppm to percentage levels and from pure metal trace analysis to high alloyed grades. All relevant elements can be directly analyzed simultaneously.
Scanning electron microscope (SEM) is an instrumental method for the examination and analysis of micro- and nanoparticle imaging characterizations of solid objects. With SEM, particle size analysis can be done to a microscopic resolution of 10 nm, that is, 100 Å.
The machine measures surface parameters and contours in one measuring run and impresses with its extremely good ratio between the measuring range and the resolution. This enables the tester to measure the slightest surface roughness and contours across a very large range—all within a single measuring run.
Metallurgical microscopes are measuring instruments for measuring thin films, electroplating coatings, grain size, surface inclusions, decarburization, case depth, structures, and defects.
Metallurgical microscopes allow the user to view opaque items at high magnification.
Design & Stimulation Capabilities
- UG NX
- Catia V5
- AutoCAD
Computer-aided design software is used to create a design with precise results, create CAD data, and validate CAD data. We have different computer-aided design software and qualified personnel for each CAD software to be able to meet the customer’s as well as various R&D projects’ requirements.
ABACUS -Simulia
Finite element analysis software is used in the product design phase to accelerate the design process and find innovative solutions to engineering problems during product design. The results that are achieved through finite element analysis are required to be validated through static and dynamic testing machines. We have our material library, which is used in FEA software to achieve the best possible analysis results.